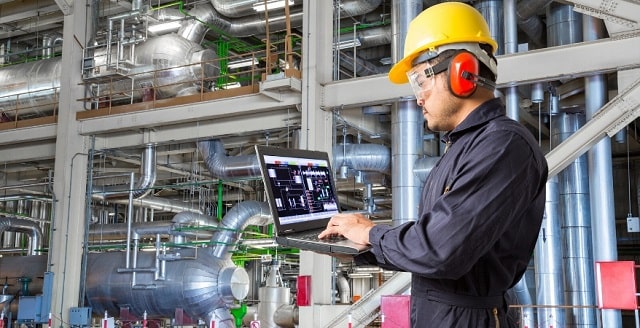
Running a manufacturing plant means that you have to be efficient in everything you do. You need to minimize your costs and maximize your output. Everything you do in your facility depends on everything else. Although 20 years ago, regular maintenance may not have been a top priority for manufacturing plants, it should now be a vital piece of your operation.
Regular maintenance means you can catch problems before or as they arrive and straighten them out before they get too big. Avoiding failures and unplanned downtimes will keep your productivity high at all times. It can also save you money since large repairs can often cost much more than it would to maintain your plant and equipment regularly. However, the fact is that poor maintenance can lead to massive problems and losses, and you need to do whatever you can to avoid that.
That said, your maintenance has to be as efficient as possible, just like the rest of your operations. Of course, making investments will be necessary, but you want to keep those as low as possible while also doing everything needed to keep things running smoothly. That involves having a plan. Here is how to create a proper maintenance strategy for your manufacturing plant.
Calculate The Cost Of Downtime
Creating a maintenance strategy requires understanding how much downtimes cost. This will help you determine how much you should invest to protect your operations properly. You will need to understand how often you are having issues and unplanned downtimes, how much it costs to repair machinery, how much parts cost, and what kind of response time you have from personnel who fix things.
From this information, you can calculate an accurate number for how much maintenance will save you. You will have more equipment availability and less unplanned downtime, and your staff will spend more time on production than sitting and waiting for repairs or issues fixes. Remember, even if your maintenance cost is slightly higher than the alternative possible costs, there is a benefit to ensuring that your clients are also satisfied.
Create A Preventive Maintenance Schedule
Maintenance timeframes are different for everything. Some machinery and equipment may need daily inspections, while others only need it yearly. Sometimes, you may need to contract professionals for your inspections and maintenance. For example, you can have HVAC specialists and plumbers come and make sure that those systems are running smoothly on a seasonal or yearly basis. You should have a clear schedule that outlines exactly when maintenance tasks need to be performed. Everyone should understand their role and take care of what they need to. Having a schedule has no meaning if nobody actually sticks to it.
Make Sure That Equipment Is Available
You never want a lack of equipment or supplies to be a reason for a lapse in your maintenance schedule. Make sure you always have tools, supplies, and parts ready to go at a moment’s notice. If a component wears down on a piece of equipment, then you want to replace it immediately instead of waiting to secure a new one. Self dumping hoppers are great for providing an easy receptacle to dispose of materials that can then be moved outside the building efficiently. If you make it simple for your staff, then they will be more likely to buy in. Ask them what they need, and make sure it is available.
Regular Updates
As a manufacturing plant, you probably have safety issues and thus have a safety committee that meets regularly. You should also have a maintenance committee that holds regular meetings or at least communicates on a set schedule. You should review your upcoming maintenance needs for the next work period and ensure that things are in place to make them happen. These meetings will ensure that you don’t miss anything and that none of your equipment or space goes too long without maintenance or an inspection.
Clear Roles
Whenever you develop a strategy, you need others on your team to carry out their parts in it. However, if it is unclear who is supposed to do what, then things will fall through the cracks. Too many of your workers will assume that it is someone else’s job, and certain tasks will get neglected. Therefore, assigning tasks to job positions rather than specific individuals is usually best. That way, when you hire someone new, you will have a record of maintenance tasks and their responsibilities as part of their job description.
Make Maintenance A Habit
In any factory or industrial setting, nobody would operate machinery without a hard hat and goggles or go onto the floor without work boots. These are habits that have been developed over time that everyone understands must be kept to stay safe and avoid employment repercussions. The same concept should apply to your maintenance tasks. Every day, machine operators should ensure that their equipment is ready and running properly. Floors and surfaces should be wiped down, and messes should be cleared up immediately. This should be second nature to your workers, which can only happen by making it a daily priority.
The thinking used to be that to get the most out of a piece of equipment, you should run it into the ground. Some factories and manufacturing plants also did not place a premium on cleaning and regular upkeep. That has all changed. To stay as productive and safe as possible, and avoid any unplanned or unnecessary downtime, ensure you have a comprehensive maintenance strategy in place.